MODULAR ROBOTIC PACKAGING MACHINES
Schubert is a family-owned company founded in 1966 by Gerhard Schubert in Crailsheim, Germany. Since the company was established, Schubert has grown to be the internationally recognized market leader for end-of line packaging machines for manufacturers of food, confectionery, drinks, pharmaceuticals, cosmetics and technical consumer goods.
Schubert packaging machines are designed from a catalogue of TLM (Top-loading machines) sub-machines. When TLM sub-machines are lined up and connected they come together to make the TLM packaging system. The smallest TLM packaging machine might consist of a single sub-machine. On average, however, TLM machines are made up of 5.5 sub-machines. Large packaging systems bring this up to 11 to 15 sub-machines, and the largest system built to date is made up of 26 sub-machines. The particular advantage of Schubert’s modular system is the ability to design the packaging machine individually to the customer’s needs.
Schubert is partnering with Winckler & Co in Japan since beginning of 2020.
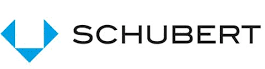
Pickerline
This is an example of a Pickerline which comprises four sub-machines. A 1,600-millimetre-wide product belt transports the baked goods along the line. At the same time, the plastic trays are destacked and placed into the chain conveyor.
During packaging, each piece of pastry is picked up individually with a suction cup, correctly oriented by the robot and placed into the tray. The manufacturer processes five different product formats, with ten products being placed into each tray. The integrated 3D scanner ensures that only perfect products are accepted. This guarantees continuous quality control.
Packingline with integrated Cartoner
A Packingline is used for creating mixed assortments. This Packingline comprises 6 infeed conveyors for 6 different type of pralines. Before the pralines are being picked by a F4 robot, they are put in the upright position by a vibration unit.
A scanner detects the position and orientation of the products and controls the quality. Only flawless pralines are placed into the provided plastic trays. Subsequently, F2 filling robots place the filled trays into erected double-wall boxes and, depending on the format, insert padding papers to protect the products.
Combination of Pickerline and Packingline
With seven TLM sub-machines, Schubert combined a Pickerline and a Packingline into a compact system. Thanks to flexible position adjustment of the pick & place robots, automatic changeover from online production, to the packaging of mixed assortments is possible.
For customised solutions such as this one, Schubert draws on its decades of experience as an innovative, market-leading manufacturer of packaging machines. This requires close collaboration with the customer – even over long distances. The machine was delivered to Australia.
Cartoner
Instead of using the conventional side-loading method for bag packers, Schubert uses the top-loading principle for these applications. The bags of biscuits are not packed from the narrow side of the carton, but instead are placed in the cartons from above through the largest possible opening.
A special feature of this packaging machine is the design of the filling tool. Instead of conventional pneumatic cylinders, the adjustable tool is equipped with NC motors. The advantage is that these motors require less maintenance than pneumatic technology. This means that the filling robot does not require a tool change for changing over to another format, and the adaptation can be carried out by simply changing the program.
Casepacker
This Casepacker carries out the final packaging process for products packed in flowpacks in varying sizes of 135, 200, 400 and 500 grams, either in shelf-ready cartons or pre-glued RSC cases. Schubert achieves this by combining a pivoting product belt, custom-designed robotic tools and an intelligent control. In this way, the flowpacks can be grouped and put in their final packaging in different orientations in the shelf-ready cartons.
Flowpacker
This Flowpacker is a fully integrated single-source solution, that offers clear potential for space savings, even better supply chain optimization and guarantees stronger service support. It consists of a picker line and a flow-wrapping component in one system. This offers higher production efficiency, maximum flexibility and the opportunity to pack new products and other formats afterwards. The format changeover required for this is quickly realized.